فولاد، مهمترین آلیاژ تولید شده در تاریخ تمدن بشر میباشد. انواع فولاد، بزرگترین حجم تولید و کاربرد را در بین تمام فلزات وآلیاژهای موجود در عصر حاضر را دارد. اما علت این موضوع چیست؟ چه چیزی باعث محبوبیت انوع فولاد در صنعت امروزی شده است؟ چند نوع فولاد در دنیا تولید شده است؟ میزان تولید سالانهی فولاد در دنیا چه مقدار است؟
در این مقاله به بررسی و پاسخ به این سوالات میپردازیم.
فهرست این مطلب
فولاد چیست؟
شاید اینطور به نظر برسد که تعریف فولاد، مفهومی ساده و پیشپا افتاده است. اما بررسی دقیقتر و علمی این مفهوم، در درک کاربردهای فولاد کمک شایانی خواهد کرد.
فولاد یعنی چه؟ در واقع آلیاژی متشکل از آهن، کربن و مقادیر دیگری از سایر عناصر است. آهن به تنهایی استحکام و سختی بسیار پایینی دارد و به آسانی در مقابل فشار، آسیب دیده و تخریب میشود. علی رغم استحکام و سختی پایین، آهن خالص چکش خواری خیلی مناسبی دارد و با نیروی کم به اشکال مختلف در میآید. برای رفع مشکل استحکام و سختی آهن، از کربن استفاده میشود. اضافه کردن کربن به آهن، در ازای کم کردن مقداری از شکل پذیری، سختی آلیاژ را تا مقادیر زیادی بالا میبرد.
تفاوت فولاد و آهن در چیست؟
همانطور که گفته شد، فولاد یک آلیاژ بر پایه آهن است که توانسته است به کمک کربن و سایر عناصر آلیاژی، استحکام و کاربرد خود را گسترش دهد در حالی که آهن، تنها یکی از عناصر جدول تناوبی مندلیف است که استحکام لازم برای کاربردهای مهندسی را نداشته و نمیتواند به تنهایی مورد استفاده قرار بگیرد. در واقع تمامی مقاطع آهنی موجود در بازار، فولادهای آلیاژی و استنلس استیل به نوعی فولاد میباشند که میزان کربن و نوع عناصر آلیاژی آنها با یکدیگر متفاوت است. لازم به ذکر است در تمامی فولادهای ساخته شده در دنیا، میزان کربن موجود در ساختار، کمتر از ۲/۱ درصد میباشد. استفاده از کربن بیش از این مقدار، منجر به تولید چدن بجای فولاد میشود.
تاریخچه فولاد
با توجه به تعریفی که از فولاد ارائه دادیم، میتوانیم بگوییم استفاده از فولاد به بیش از ۱۰۰۰سال قبل از میلاد مسیح برمیگردد. دورهای تاریخی که با نام عصر آهن شناخته میشود، سرآغاز تحول زندگی بشر امروز به کمک فولاد است. پس از آن، استفاده از فولاد، رفته رفته توسعه بیشتری پیدا کرده و انسانها یاد گرفتند که چگونه میتوانند از آهن برای ساخت ابزار کشاورزی و ادوات جنگی خود بهره ببرند.
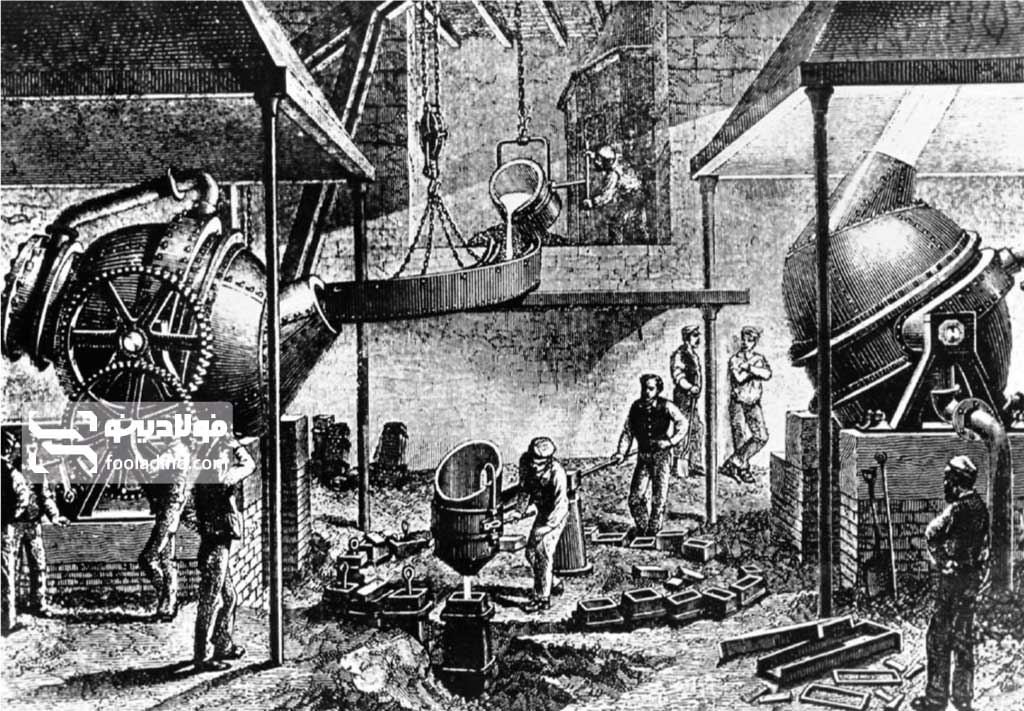
اما تولید انبوه فولاد به روش مدرن به سال ۱۸۵۰ میلادی برمیگردد. جایی که هنری بسمر، دانشمند بریتانیایی توانست تکنیک موثری را برای ذوب و تولید فولاد ارائه کند. این روش، بعدها به اسم خود او نامگذاری شده و به روش بسمر معروف است. در این روش، ناخالصی با کمک دمش هوا به سرباره اضافه شده و از ذوب خارج میشود. شکل کورههای ابتدایی روش بسمر را در تصویر زیر مشاهده میکنید.
انواع فولاد
فولاد با توجه به خواصی که دارد، میتواند از نقطه نظرهای متفاوتی تقسیم بندی شود. یکی از این دستهبندیها جداسازی فولاد بر اساس مقدار کربن موجود در ساختار است.
۱) انواع فولاد بر اساس مقدار کربن
بر اساس این تقسیمبندی، سه دسته عمدهی زیر برای فولادها تعریف میشود:
- فولاد کم کربن
- فولاد کربن متوسط
- فولاد پر کربن
هر کدام از دستههای بالا، خواص و ویژگیهای منحصر به فرد خود را دارند که در ادامه به هر کدام از آنها میپردازیم.
+) فولاد کمکربن
فولاد کمکربن دسته مهمی از فولادها به حسب میآیند که میزان کربن در ساختار آنها، کمتر از ۰/۳درصد میباشد. وجود مقدار کم کربن در این دسته از فولادها، باعث ایجاد خاصیت انعطافپذیری و شکلپذیری بسیار بالا، نسبت به سایر دستهها شده است. علاوه بر این خاصیت، فولادهای کم کربن، عموما مقاومت به خوردگی ضعیفی دارند.
نکته قابل تامل در خصوص فولادهای کمکربن، قیمت پایین این دسته میباشد. وجود مقدار کم کربن و عناصر آلیاژی علاوه بر کاهش هزینه ناشی از نبود عناصر آلیاژی، به دلیل سادگی فرآیند ساخت، قیمت محصول نهایی را کاهش میدهند.
+) فولاد کربنمتوسط
فولاد کربنمتوسط دستهای از فولاد است که کربن آن بیش ۰/۳ درصد و کمتر از ۰/۸ درصد باشد. ویژگی بارز این دسته از فولادها این است که برای سختکاری به دمای کاری پایینتری نیاز است و این به معنای بهبود شرایط عملیات حرارتی و کاهش میزان مصرف انرژی میشود.
+) فولاد پرکربن
فولاد پرکربن به دلیل دارا بودن مقدار زیادی کربن در ساختار خود، سختی بسیار بالایی را از خود نشان میدهد، اما از سویی دیگر، هرچه میزان کربن در ساختار بالاتر میرود، انعطافپذیری فولاد کاهش پیدا میکند، به طوریکه به عنوان مثال در فولادهای با بیش از ۲ درصد کربن، مقاومت به ضربه شدیدا کاهش یافته و فولاد مورد نظر ترد میشود. درصد کربن در این دسته از آلیاژها، بین ۰/۸ تا ۲/۱ است.
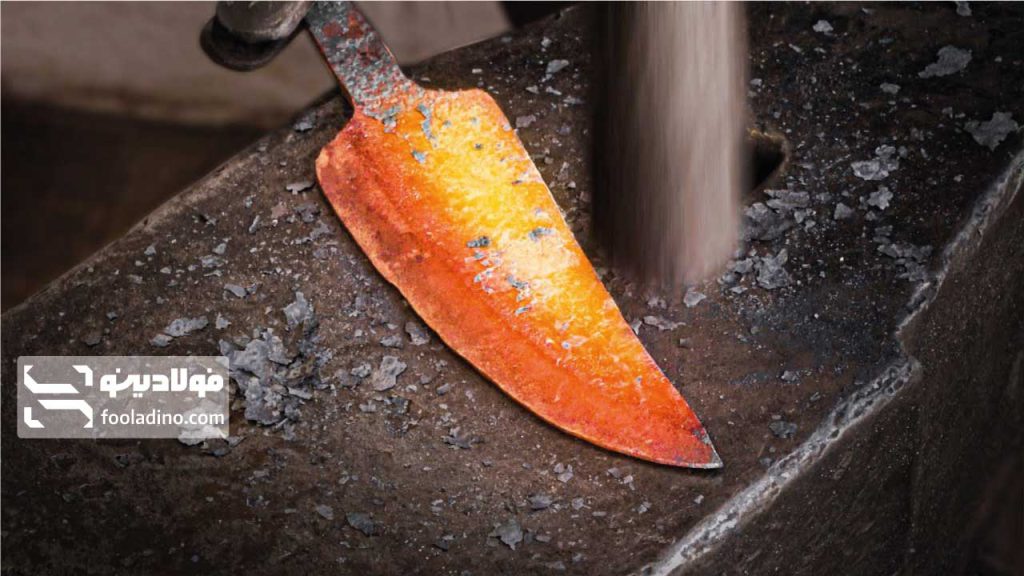
۲) انواع فولاد بر اساس روش ساخت
یکی دیگر از روشهایی که به وسیلهی آن، فولادها را دسته بندی میکنند، استفاده از معیار روش ساخت فولاد است. متد ساخت فولاد نظیر استفاده از تکنیکی ریختهگری مداوم یا نوع کوره مورد استفاده نظیر مقاوتی یا قوسی بودن آن، شدیدا بر خواص قطعه نهایی تاثیر میگذارد و طبیعی است که پیش از استفاده از یک فولاد مشخص، بررسی کردن این عامل، بسیار حیاتی است. علاوه بر مرحله شمشریزی، روشهای ساخت نهایی نظیر نورد گرم، نورد سرد و شرایط کشش قطعه نیز معیاری برای طبقهبندی به حساب میآید.
بیشتر بخوانید: تفاوت فولاد نورد گرم و نورد سرد چیست؟
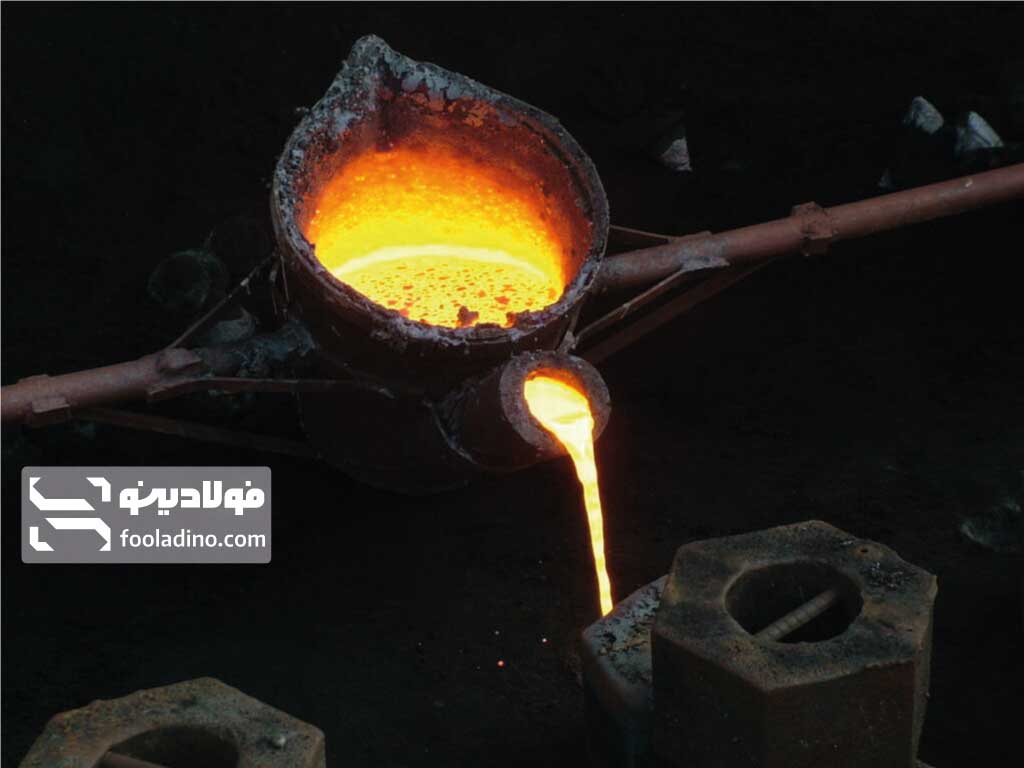
۳)انواع مقاطع آهن آلات
تقسیمبندی انواع فولاد بر اساس سطح مقطع آن، یکی از معتبرترین دستهبندیها در سطح بازار به شمار میآید. همانطور که در صفحه اول وبسایت فولادینو قابل مشاهده است، آهن آلات میتوانند به دستههایی نظیر میلگرد، ورق، قوطی پروفیل، تیرآهن و لوله تقسیم شوند که هر دسته، مجددا بر حسب نیازهای مشتری، به زیر دستههای دیگری تقسیم شده اند.
۴) انواع فولاد بر اساس ریز ساختار
شاید بتوان گفت یکی از دقیقترین و صحیحترین دستهبندیهای مورد استفاده برای تفکیک فولادها، مراجعه به ریز ساختار آنهاست. بخش زیادی از رفتارهای هر فلز، متاثر از نوع ریز ساختاری است که در آن شکل گرفته است. در مورد فولاد هم، شرایطی مانند مارتنزیت یا پرلیتی بودن و همچنین اندازه دانههای میکروسکوپی باعث تفاوت ریز ساختاری و شکل گیری این نوع از دسته بندی میشوند.
۵) عملیات حرارتی
عملیات حرارتی جزئی ناگزیر از فرآیند تکمیل ساخت یک فولاد است. میتوان اینگونه گفت که تقریبا هیچکدام از فولادها پیش از عملیات حرارتی مناسب با خود، مورد استفاده قرار نمیگیرند. گستردگی طیف عملیات حرارتی نظیر دمای گرم کردن، دمای پیش گرم، سرعت سرد کردن، محیط سرد کردن و عناصر اضافه شدن در حین عملیات، برای هر گروه از فولادها متفاوت بوده و میتوان آن را یک معیار مناسب برای طبقهبندی فولادها در نظر گرفت.
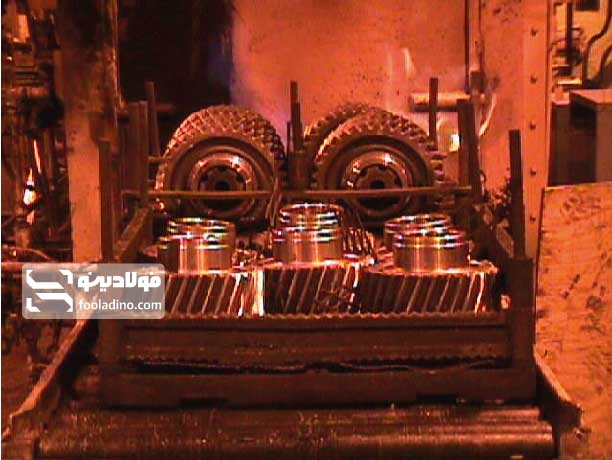
۶) انواع فولاد براساس استحکام فیزیکی
یکی دیگر از عواملی که منجر به دستهبندی فولادها میشود، میزان استحکامی است که هر فولاد متناسب با استاندارد ASTM از خود نشان میدهد. این استحکام میتواند به دو دسته استحکام تسلیم و استحکام کششی برای هر فولاد تقسیم شود. در واقع برای ارزیابی عیار هر فولاد، خوانش این دو پارامتر ، بسیار مهم است.
نامگذاری فولادها
برای نامگذاری فولادها دو منبع استاندارد جهانی تعریف شده است. سیستم نامگذاری اولی که توسط انستیتو آهن و فولاد آمریکا وضع شده است، AISI نام دارد. و سیستم دیگر که توسط انجمن مهندسان اتومتیو نامگذاری شده است به اختصار SAE نام دارد. هر دو سیستم برای نامگذاری فولادهای خود از کد اعداد 4 رقمی کمک میگیرند که در آن هر عدد نشان دهنده میزان کربن یا سایر عناصر آلیاژی در ساختار آن فولاد مورد نظر است. همچنین برخی دستهبندی فولادی وجود دارد که با کد 5 رقمی نشان داده میشود.
اگر کد فولادی در هر دو استاندارد با رقم 1 شروع شود، فولاد معرفی شده در دسته فولاد کربنی قرار میگیرد. سایر رقمها نیز به معنای عناصر آلیاژی زیر است:
رقم | گونه فولاد مورد بررسی |
---|---|
2 | فولاد نیکل دار |
3 | فولاد نیکل- کروم دار |
4 | فولاد مولیبدن دار |
5 | فولاد کروم دار |
6 | فولاد وانادیوم-کروم دار |
7 | فولاد تنگستن-کروم دار |
8 | فولاد نیکل-کروم-مولیبدن دار |
9 | فولاد سیلیکون-منگنز دار |
رقم دوم هم نشان دهنده درصد عنصر آلیاژی غالب در آن آلیاژ بوده و دو رقم نهایی هم نشان دهنده میزان درصد کربن در آن فولاد است.
به عنوان مثال، فولاد SAE5130 نشان دهنده فولاد کروم دار با حدود 1 درصد کروم و 0.3 درصد کربن است.
فولاد آلیاژی چیست؟
علی رغم تمام مزایای انواع فولاد متداول، نظیر سختی و استحکام بالا، شکلپذیری مناسب و هدایت حرارتی و الکتریکی قابل قبول، فولادها عموما مقاومت به خوردگی مناسبی ندارند. همچنین گاهی نیاز به سختی و استحکام بالاتر وجود دارد.
اضافه کردن عناصر آلیاژی میتواند با افزایش سختیپذیری فولاد، استحکام و سختی آن را بالا ببرد. همچنین استفاده از عناصر آلیاژی، این امکان را به فولاد میدهد که بتواند در دمای کاری بالا نیز مورد استفاده قرار بگیرد. از جمله عناصر آلیاژی پرکاربرد در ساخت فولاد آلیاژی میتوان به کبالت، کروم، نیکل، مولیبدن و تنگستن اشاره کرد.
جهت دریافت اطلاعات بیشتر درباره فولاد ضد زنگ میتوانید مقاله فولاد آلیاژی چیست را مطالعه کنید.
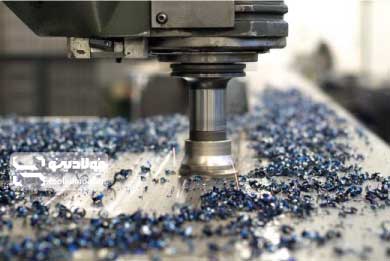
فولاد زنگ نزن (استنلس استیل)
همانطور که میدانید، فولادهای متعارف موجود در دنیا دارای یک عیب مهم هستند و آن ضعف در مقاومت به خوردگی فولاد است. این امر، بسیار حیاتی است چرا که بر اساس محاسبات صورت گرفته مشخص شده است که حتی در کشورهای بسیار پیشرفته، حدود ۵ درصد از تولید ناخالص ملی، صرف هزینههای ناشی از خوردگی میشود. این عدد، در کشورهای در حال توسعه و جهان سوم به مراتب بالاتر است. دانستن این نکته، مشخص میکند که توانایی ایجاد خاصیت مقاومت به خوردگی در فولادهای تولید شده، تا چه اندازه میتواند به اقتصاد یک کشور کمک کند.
فولاد ضد زنگ دستهای از فولادهای نسبتا جدید در دنیا میباشد که توانسته است به کمک عناصر آلیاژی نظیر نیکل، کروم، کبالت و مولیبدن، تا حدود مناسبی، به فولاد تولید شده، خاصیت مقاومت به خوردگی را ببخشد.
فولادهای ضد زنگ یا همان استنلس استیل در حال حاضر، هزینههای تولید بالایی دارند و قیمت آن برای مصرفکننده بسیار بیشتر از فولادهای معمول میباشد. به همین دلیل، همچنان در کاربریهای غیر حساس از فولادهای معمولی استفاده میشود.
از جمله مهمترین فولادهای زنگ نزن میتوان به استیل ۳۰۴، استیل سری ۴۳۰ و استیل نسوز اشاره کرد.
مشکلات فولاد سازی
وجود مشکلاتی نظیر حساسیت به خوردگی و همچنین وزن بالای فولاد، نیاز به ساخت فلادهای با خواص برتر را الزامی کرده است. اما آنچه باعث میشود، ساخت فولادهای جدید با محدودیتهای تولید مواجه شود، و به تبع آن هزینههای تولید بالاتر رود را میتوان در کلمات زیر جست:
- شناوری و ته نشینی
- جدایش غلظتی
- ضخامت مقطع تولیدی
۱) شناوری، ته نشینی و جدایش غلظتی
استفاده از عناصر آلیاژی مختلف در ذوب فلزی همواره با یک مشکل عمده روبرو است و آن، اختلاف وزن مخصوص آهن و عنصر آلیاژی مورد استفاده است. عنصر آلیاژی سبکتر به روی ذوب آمده و وارد سرباره میشوند و از خواص مد نظر شمش فاصله میگیرد. عنصر سنگینتر نیز در کف پاتیل ته نشین شده و مشکل ذکر شده را به طریق مشابهی تکرار میکند. هر دوی این عوامل، باعث جدایش غلظتی در شمش نهایی میشود.
۲) ضخامت مقطع فولاد
بحث ضخامت مقطع تولید شده از دو جهت اهمیت دارد. مورد اول، همانطور که در بالا نیز گفته شده است، مربوط به جدایش غلظتی میشود. هرچه مقطع ضخیمتر باشد، کنترل خواص سختتر میشود.
مورد و مشکل دوم مقاطع ضخیم، کاهش احتمال سخت شدن فولاد، در مرکز خود میباشد. هرچه نمونه ضخیمتر میشود، به دلیل کمتر شدن تماس با محیط خنک کننده مانند آب، انتقال حرارت با سرعت کمتری انجام شده، و مرکز فولاد، سخت نمیشود.
۳) نبود تجهیزات و امکانات به روز
برای تولید برخی فولادهای مشخص، نیاز به خلوص بسیار بالا و حذف حداکثری عناصری نظیر گوگرد و فسفر است. تهیه کورهایی با قابلیت تصفیه بالای این عناصر گاهی اوقات بسیار گران بوده و صرفه اقتصادی ندارد.
وجود این عوامل باعث شده است که علی رغم تولید فولادهای متعارف به روشهای کوره بلند و احیای مستقیم، در کارخانجاتی نظیر ذوب آهن اصفهان و فولاد خوزستان، امکان تولید برخی فولادها در حال حاضر در کشور مهیا نباشد.
کاربرد فولاد چیست؟
در حال حاضر، فولاد پرکاربردترین فلز در صنعت روز دنیا میباشد. شاید برایتان جالب باشد که بدانید فولاد در سال گذشته به تنهایی ۹۲ درصد از سهم صنعت فلزات دنیا را به خود اختصاص داده است به طوری که در سال ۲۰۱۹ میزان تولید فولاد به عدد ۱۸۷۰ میلیون تن رسیده است. این فولادها در ۳۵۰۰ گرید مختلف در دنیا تولید شدهاند. هر کدام از دستهبندیهای معرفی شده در این مقاله میتوانند بخش زیادی از تولید سالانه فولاد را به خود اختصاص دهند. مشاهده میشود، فولاد از کاربریهای پیش پا افتاده تا صنایع بسیار حساس، میتواند مورد استفاده قرار بگیرد. صنایع ساختمان سازی و عمرانی، صنایع تولید اتومبیل، صنایع مرتبط با استفاده از انرژیهای تجدیدپذیر و صنایع هستهای از جمله مهمترین کاربردهای فولادها در دنیا میباشند.
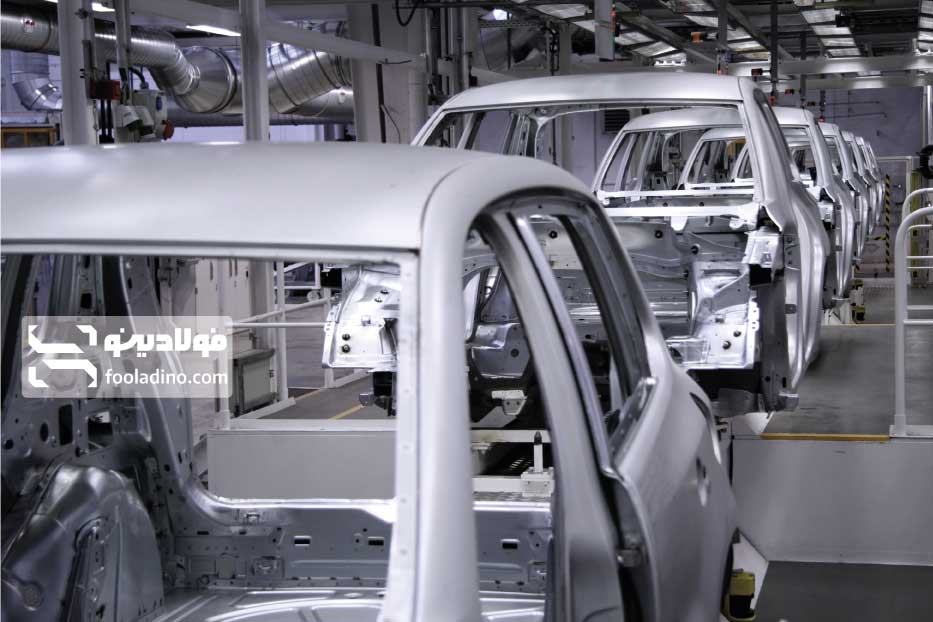
برای تصدیق مطالب فوق و استفاده از منبع اصلی اینجا کلیک کنید.
حال سوالی که پیش میآید این است که آیا فولاد میتواند همچنان بیشترین سهم را داشته باشد؟
مهمترین کارخانههای تولید فولاد در ایران
برای شناخت مهمترین کارخانههای موجود در ایران، نیازمند این هستیم که بدانیم طبقه بندیها بر چه اساسی انجام میشوند. برخی از کارخانجات داخلی همانند فولاد خوزستان، تنها به تولید محصولات اولیه نظیر تختال میپردازد. از طرفی، اگر فاکتور حجم تولید مورد بررسی قرار بگیرد، کارخانههایی مانند ذوب آهن اصفهان از اهمیت بالایی برخوردار هستند. همچنین؛ فولاد مبارکه اصفهان به لحاظ تنوع در تولید ورقهای فولادی در صدر تولید کنندگان کشور قرار دارد. فولاد آلیاژی اسفراین و فولاد آلیاژی یزد نیز از جمله مهمترین تولید کنندگان فولادهای آلیاژی در کشور به حساب میآیند.
آینده صنعت فولاد
پیشرفت علم و ظهور دستهی جدیدی از مواد تحت عنوان کامپوزیتها توانسته است پتانسیل بسیار بالایی را از خود نشان دهد تا در موارد زیادی به عنوان فولادها مورد استفاده قرار بگیرد. این مواد وزن پایینی دارند و مقاومت به خوردگی عمدتا بالایی دارند. اما فولادها همواره به عنوان یک ماده برتر مهندسی شناخته میشوند و جایگاه خود را میتوانند حفظ کنند.
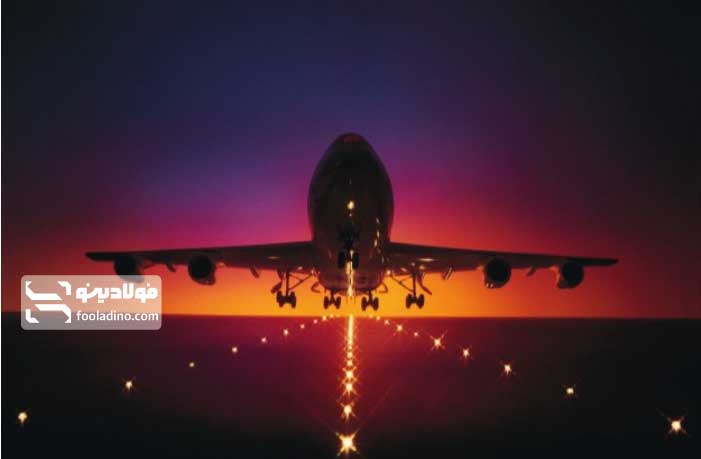
پس برای پاسخ به این سوال میتوان اینگونه گفت که، علی رغم اینکه به نظر میرسد انواع فولاد که به شکل امروزی مورد استفاده قرار میگیرند، جایگاهی در آیندهی صنعت دهههای آینده نخواهند داشت، اما با توجه به پتانسیل بالای خود، حتما از آنها در ساخت مواد جدید استفاده خواه شد و فولاد با چهرهای متفاوت همچنان یکهتازی خواهد کرد.